Are you considering switching to artificial grass but first want to know how it compares with natural grass in the key areas of cost, maintenance, health and safety, and so on?
Not all turf is created equal so we need to understand how artificial turf is made. What materials go into the best synthetic grass and what does the manufacturing process involve?
Artificial turf in 2024 is very different from its first incarnations used in commercial applications in the 1960s and 1970s. Many perceived drawbacks have been corrected by improved technology and manufacturing processes—so much so that the best turf now is almost distinguishable from the real stuff.
Let’s look at how artificial grass is made—the manufacturing process and materials that go into it—and what to look out for when selecting turf for your backyard or commercial project.
HOW ARTIFICIAL TURF IS MADE: BASICS
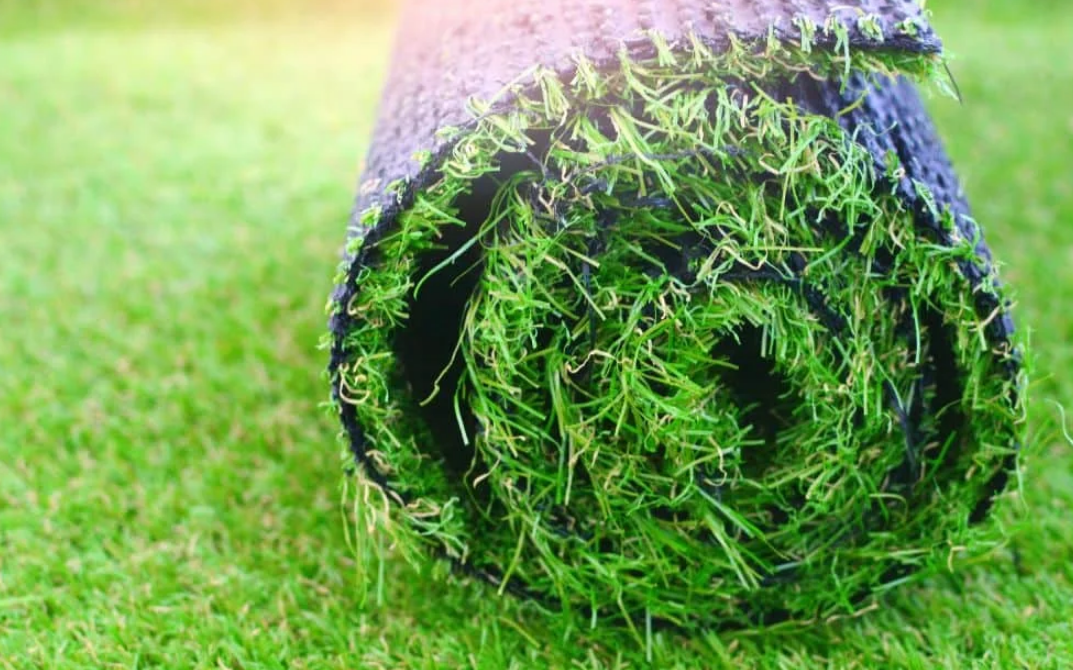
Turf used in the U.S. is made predominantly from polyethylene (PE), polypropylene (PP) or nylon fibers machine-stitched into a backing material in large production facilities using giant tufting machines. A second backing layer of adhesive provides extra strength and holds the turf fibers in place in the best quality turf. The end product is sold in large rolls in major retailers, home improvement stores, and dedicated turf suppliers. This production method is similar to how mass-produced carpets are traditionally made.
Manufacturing processes, materials, and precise compositions of the artificial turf vary from facility to facility—and also vary with the quality and intended usage of the turf (some turf requires extra durability to handle heavy traffic or wear and tear from sports players, for instance).
ARTIFICIAL TURF: A DEEPER LOOK AT THE MANUFACTURING PROCESS
Artificial turf is used increasingly as a replacement for natural grass in backyards across the U.S. as well as in many amateur, college, and NFL sports fields, and other commercial enterprises.
Understanding the manufacturing process can help shed light on the different qualities of turf available, as well as its environmental impact.
The two main components of all artificial grass are the turf fibers that make up the “blades of grass” and the backing into which it is machine-stitched. What is the process that makes the turf so closely resemble the real thing?
Here’s a rundown of the stages of the traditional turf-making process…
1. Coloring the plastic pellets
Turf production generally starts with large bags of high-quality white plastic granules or pallets.
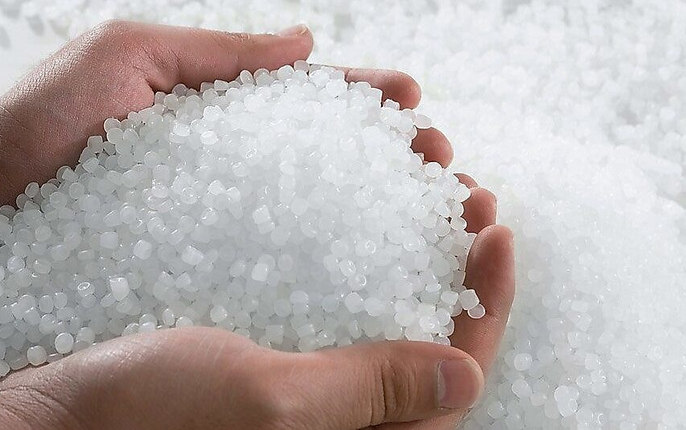
These pellets are melted down and colored green with the addition of dye. The precise color (emerald, olive, field, lime, and forest are the most common shades) will depend on the intended use of the turf—putting green turf is usually a different hue to lawn turf, for instance. Chemical stabilizers are also added to the mix at this point.
2. Shaping the plastic yarn
The melted mixture is forced through steel dies with holes in them to create the long blade-like strands of material that will form the turf blades. This process is called “extrusion” and it can be varied depending on whether fibrillated or monofilament yarn is required. Fibrillated yarn is more traditional and created as a tape (strands), while monofilament yarn allows for different blade shapes and requires a different dye to be used.
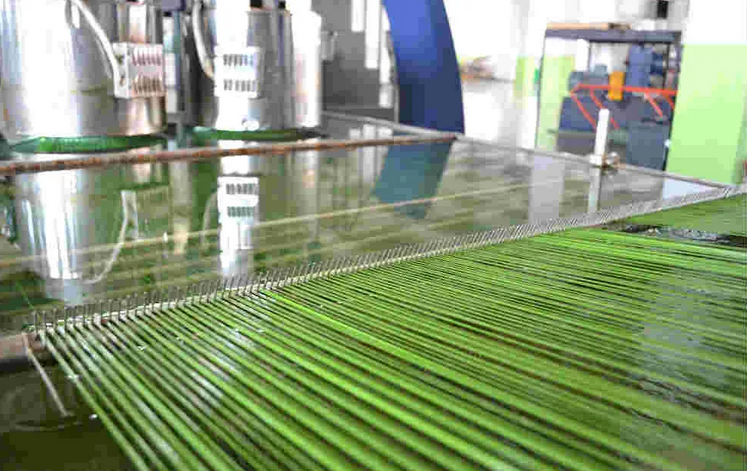
3. Cooling and stretching
The strands of plastic are cooled in water and kept separate using large comb-like machinery before the strands are stretched and strengthened using rollers. During this process, the plastic strands become as fine as real grass blades.
4. Spooling of the yarn
In the traditional manufacturing process for fibrillated yarn, large spooling machinery rolls up the synthetic turf strands to the required spool size before it is removed. The plastic strands from multiple spools are unwound to form a multi-ply synthetic yarn, which is rewound into a larger spool.
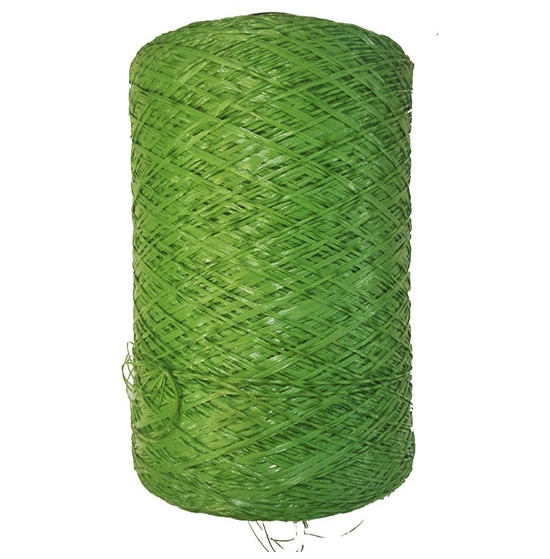
5. Preparing to stitch
The multi-ply yarn travels through tubing to a tufting machine, which is essentially a giant sewing machine with hundreds of needles. Elsewhere in the production process, mesh fabric is usually joined to synthetic sheeting to form the primary backing,
6. Stitching and cutting the yarn
The needles in the tufting machine rapidly stitch the yarn through the synthetic sheeting into loops. The artificial turf is created upside down. So, beneath the sheet, the individual pieces of looped yarn are cut to the required length to resemble real grass.
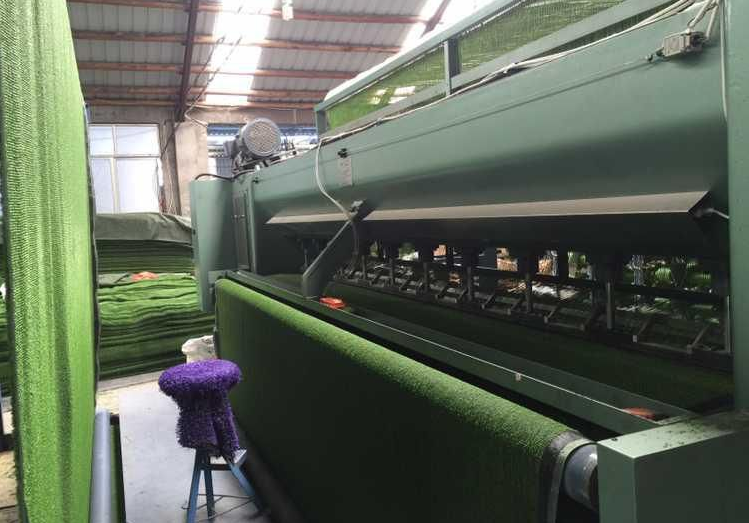
7. Coating the turf with adhesive
The turf is examined for uniformity of yarn length before it is sent to a coating roller, which collects adhesive (the secondary backing material) from a trough and applies it to the primary turf backing. This helps to bind the yarn and backing components of the turf.
8. Drying and perforating
After the adhesive is dried by placing the turf on large drying machinery, the turf is pierced by hot pins that make it permeable to liquids (important for artificial grass drainage).
9. Inspection and quality control
As with any high-quality product made in a factory, the artificial turf is inspected to make sure that it looks and feels its best. Loose pieces are removed and the fiber length is measured to ensure accuracy. Another essential part of the manufacturing process is to stress test the turf to ensure that it is of the required durability for the intended purpose.
10. Wrapping, packing, and shipping
Once everything meets the required standards, the rolls of turf are tightly wrapped, packed, and sent around the country to turf suppliers and retailers—or exported.
If you’d like to know more about how artificial turf is made, here’s a popular video that explains the traditional manufacturing process of sports field turf: Insert video using embed code below but only if it truly reflects the process used to create DFW/AGP turf.
Variations to the turf manufacturing process
The above describes the traditional artificial turf manufacturing process.
This process varies from turf type to turf type. For instance, a layer of thatch is often added to the most realistic turf brands. This is a layer of curly brownish or yellowish grass that resembles dead grass to make the turf appear more realistic.
The use of monofilament or fibrillated yarn also causes variations in the manufacturing process. Many of the best artificial grass types use different-shaped blades that impart different properties to the turf. The most common blade shapes are outlined here:
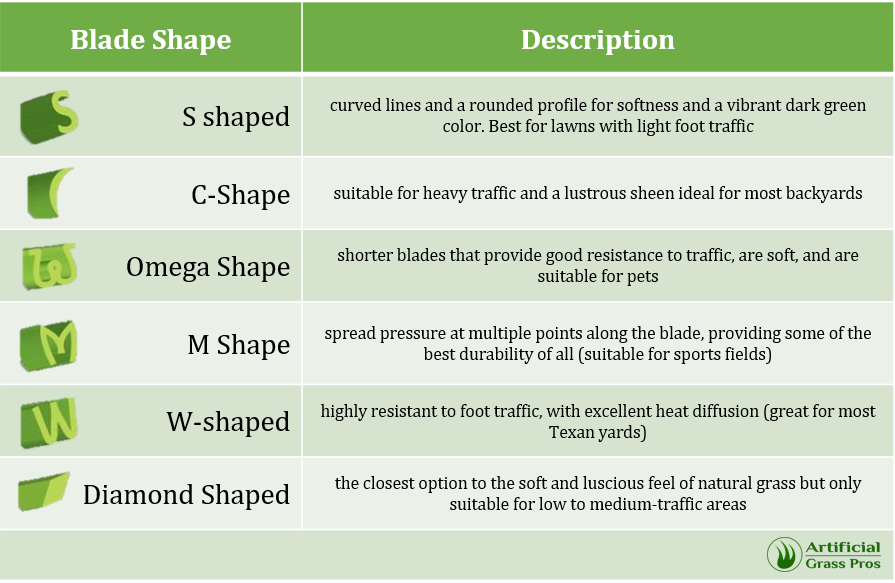
Different features can be added to the turf as an “in-line” process, or as a second stage where the yarn is texturized on separate machinery.
WHAT MATERIALS ARE USED IN ARTIFICIAL TURF?
Let’s take a closer look at the materials used to make artificial turf—including the main blades and the backing.
MAIN TURF MATERIALS
Three main materials are used to create the turf blades:
Polypropylene (PP)
Polypropylene is cost-effective and feels soft as artificial turf but there are question marks over its durability, especially in higher temperatures.
Polyethylene (PE)
Polyethylene has a natural “grassy” appearance and a soft texture. It is more durable than polypropylene and performs better at higher temperatures and with heavy foot traffic.
Nylon (PA)
Nylon (or polyamide) is sometimes chosen for artificial sports turf because of its high durability compared to other available materials. It is usually more expensive and less soft to the touch because of its stiffer blades.
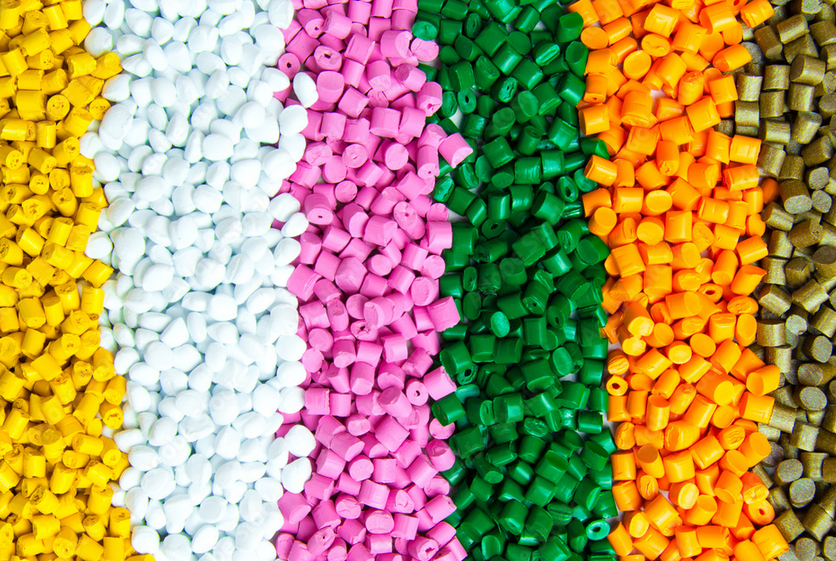
MAIN BACKING MATERIALS
The other materials used in artificial turf are those that make up the backing. These are critical to the stability, durability, and performance of the turf.
In the best quality artificial grass, backing refers to two components of the turf:
- Primary backing: the sheet/mesh that the turf fibers are tufted into.
- Secondary backing: a flexible coating that adds adhesiveness and helps hold it all together.
What is dual-layered non-expansive backing?
Some of the best-quality artificial turf uses dual-layered non-expansive backing as the primary backing material. Two layers of backing material provide added strength and durability. Polyurethane adhesive ensures that the turf maintains its structural integrity even with heavy traffic and allows good drainage even in adverse weather conditions.
Polyurethane
Polyurethane (PU) is often used as a secondary backing material for top-quality artificial turf because of its great durability, stability, and longevity. This flexible adhesive is suitable for high temperatures and high foot traffic and allows good drainage.
Latex
Latex is another commonly used secondary backing material.
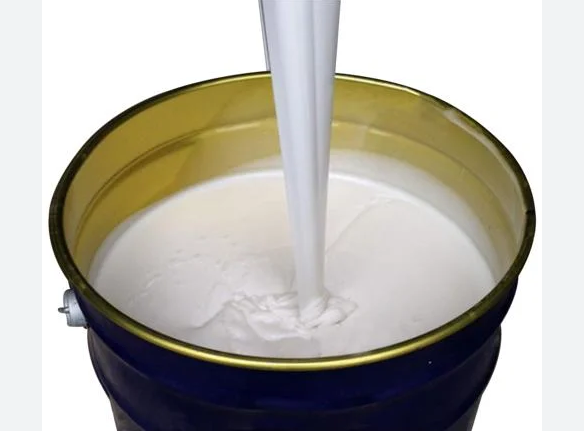
This natural rubber material is a flexible, affordable, water-based adhesive, it is applied to the underside of the turf, solidifying as it dries. Latex is not as durable as PU, can impact drainage, and may be used in inferior quality turf unsuitable for high temperatures.
WHAT’S CHANGED SINCE THE 1960s?
Artificial turf was invented in the 1960s and has come a long way since then. Many of the criticisms leveled at artificial turf refer more to the old-style turf than modern products—and, at the same time, the benefits of artificial turf have been increased.
In the 1960s, nylon-based artificial grass started to appear extensively—especially on sports fields where low-maintenance solutions were sought to replace high-maintenance grass that was difficult to grow and keep in shape.
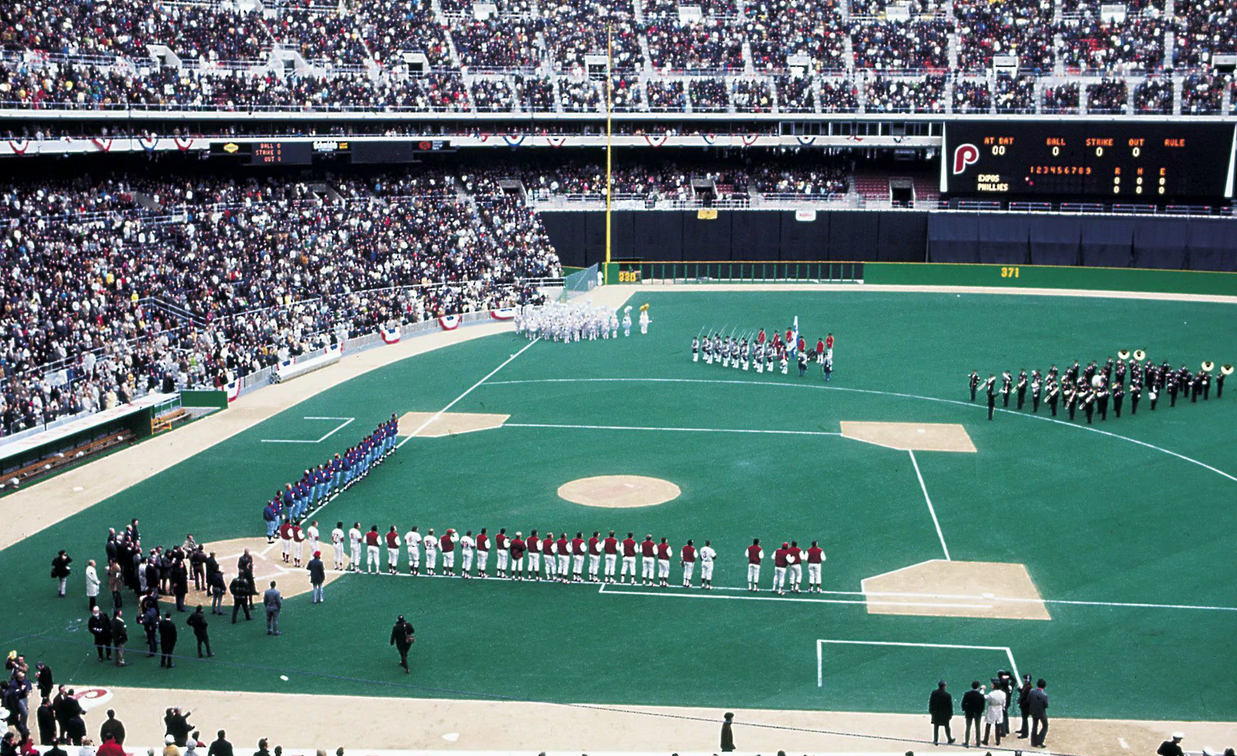
Polypropylene turf started to appear in the 1970s and 1980s, along with low-density polyethylene (LDPE) turf.
Nowadays, most high-quality turf is made from high-grade polyethylene (PE) because it offers an ideal balance between durability, aesthetics, and softness. Higher-grade PE is more expensive but aids the durability of the turf.
In the past decade or two, polyethylene monofilaments have started to revolutionize artificial turf with greater softness, less abrasiveness, and a more natural look, as well as greater durability. Not only are most of the artificial grass NFL fields now made using this technology but it is also used in turf for backyard lawns, pet turf, turf strips around backyard swimming pools, and more.
The manufacturing process for turf remains similar in many ways but advances have been made to make it faster and more efficient. The end product has been greatly improved since the early days of turf—in many aspects:
- Potential toxicity and impact on human health: heavy metals like lead were once used extensively in artificial grass but these have been eradicated, as have PFAs (perfluoroalkyl and polyfluoroalkyl substances, known as “forever chemicals”).
- Blade shape (highlighted above) provides different qualities, with added durability, texture, cooling, qualities, etc. S-shaped, W-shaped, and other shaped blades are now quite common in better-quality artificial grass.
- More realistic appearance and softness similar to real grass (rather than the rough and abrasive nylon feel of early artificial sports fields).
- Less shiny, more resistant to UV light, and less likely to fade.
WHY IS ARTIFICIAL TURF SO POPULAR NOW?
Artificial grass looks green and pristine all year round with next-to-no effort— even in areas where grass struggles to grow. These are the main benefits of artificial turf compared with natural grass.
Other benefits that help to account for the explosion of interest and installations in backyards, sports fields, and commercial ventures across the U.S. in recent years include:
- Ultra-low-maintenance (no mowing, fertilizing, pesticides, aerating or weed killing).
- No water required—better for drought-stricken areas.
- Flexibility—can be used for landscaping backyards, kids’ playground flooring, backyard putting greens, dog runs, around swimming pools, and for sports fields/commercial premises.
- Cost-effective—pays back the initial investment after around five years.
- Long lifespan—up to 15 or 20 years if you look after it.
- The all-weather surface makes it suitable for lawns as well as sports venues.
- May increase home value.
FAQs
Where is artificial turf made?
Artificial grass is manufactured in China and Europe (particularly Holland, Germany, the UK, Italy, and Belgium) but also right here in the U.S. For instance, most of the 15 NFL fields that have artificial turf fields use premium turf from major manufacturing facilities in Georgia and Texas.
Is artificial grass bad for the environment?
Check out our post on whether artificial grass is bad for the environment. There are pros and cons of turf and real grass when it comes to eco-friendliness. The major concerns over turf usually involve the disposal of unwanted turf and the carbon footprint but benefits include lower use of water, fossil fuels, toxic chemicals, and more.
Are there health and safety concerns with artificial grass?
Some health and safety concerns have been voiced about synthetic turf, such as heat stress, increased chance of injury, allergies, and toxic exposure. However, these generally relate to low-quality turf or older turf types. Turf does get hotter in the summer than real grass but our turf maintains manageable temperatures using cooling technology. It’s also free of toxic chemicals, allergy-free (no latex or other allergens), and installed professionally to minimize the risk of injury.
Is your turf made in the U.S.?
Yes, Artificial Grass Pros use only premium turf that employs leading-edge manufacturing practices, resulting in an elite-level turf product that performs superbly and lasts the distance.
How is infill made?
Infill helps the artificial turf more closely resemble the appearance of natural grass. Depending on the intended usage of the turf, infill is usually made of sand/silica, crumb rubber (recycled tires) or zeolite. Occasionally, you may see other products like EDPM, cork or coconut used as infill. The manufacturing process depends on the type of infill.
Considering the switch to artificial turf?
Discuss your options with an artificial grass professional.